探討定位系統量測學:原理、方法與效能提升策略
掌握量測原理與補償技術,突破奈米級運動效能瓶頸
作者:RJ Hardt,Peak Metrology 總裁
本白皮書重點在闡釋定位系統量測 (positioning system metrology) 的核心概念、其在工程上的重要性、具體的執行方法,以及如何有效運用量測結果;執行精密量測的主要目的,在於確保設計師所規劃的定位系統,於實際機械組裝完成後,能夠精確符合一系列預設的技術規格;以下內容將特別聚焦於採用閉迴路控制 (closed loop control) 機制的精密電動定位器。
何謂運動量測學?
運動量測學 (Motion metrology) 可視為一門應用科學,其核心在於定義並量測設計師所關心的各種效能指標數值;此學科使工程人員得以驗證一個機電定位系統在設計階段 (as-designed) 與實際建構完成 (as-built) 之間的具體差異;此驗證過程需透過各式量測技術,對依實作系統 (as-built system) 進行實際量測;圖 1 即呈現了此流程的初步階段。
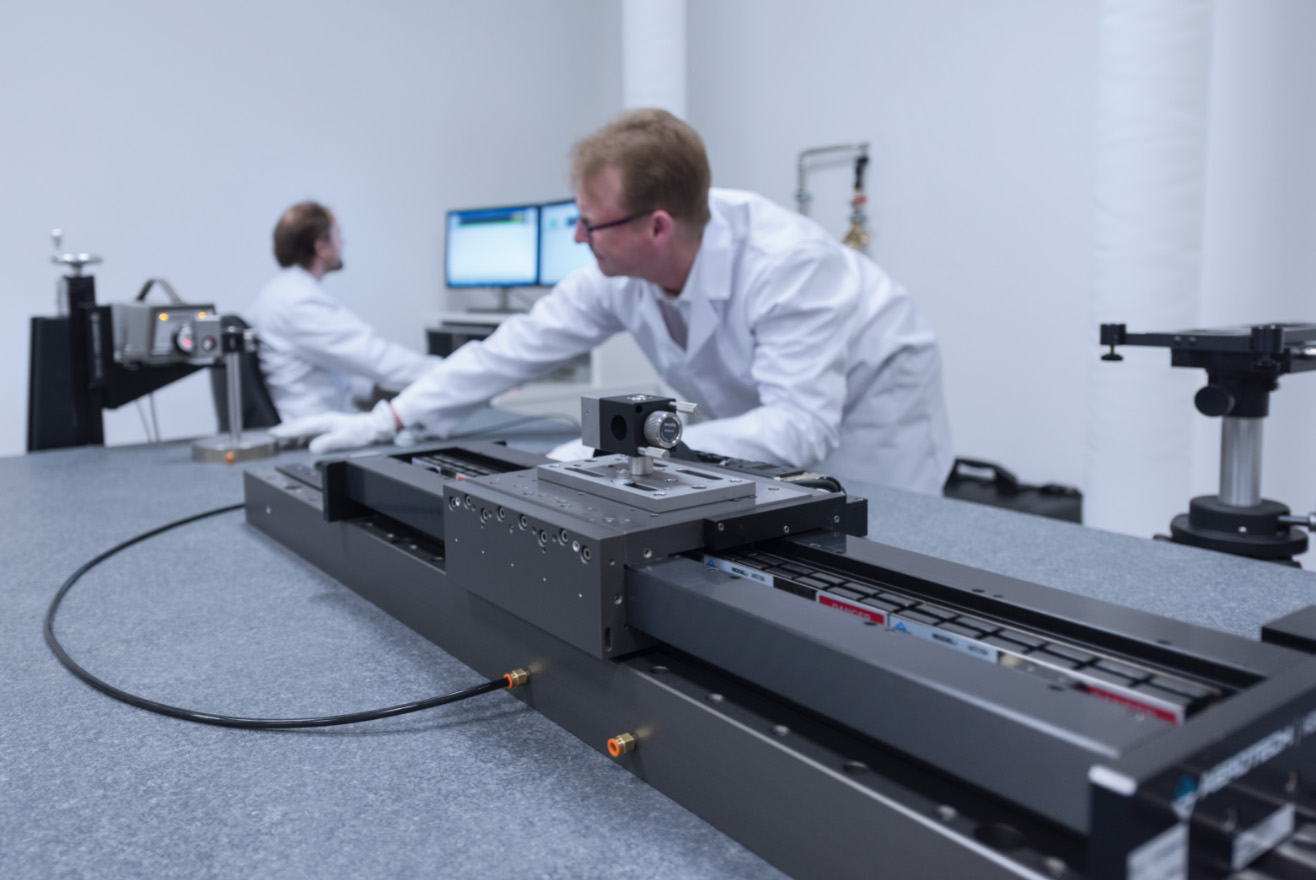
了解透過量測學所量測的內容
簡化來說,運動量測學是用來評估一個定位系統在實體空間中,從 A 點移動至 B 點的「精確程度」;實際上,沒有任何電動定位系統能夠達成完美的點對點移動;運動過程中所出現的不完美性,源自於依實作定位系統中固有或客觀存在的各種誤差來源 (error sources)。
由於運動發生於三維實體空間,因此可運用不同方法,將定位系統的實際幾何效能與特定的數學座標框架建立關聯;其中一個普遍採用的方法是利用笛卡兒座標系 (cartesian coordinate frame),將系統運動對應至空間中的一個特定點;此空間點可依設計需求在多個自由度 (DOF) 上移動,然而,每增加一個所需的運動自由度,便需要額外配置一個對應的機械定位軸。
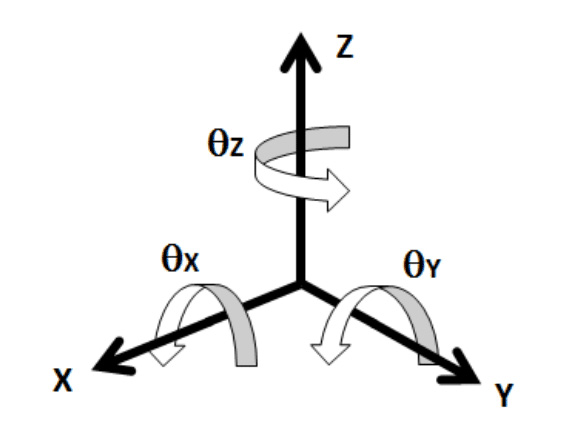
圖 2. 笛卡兒座標框架,顯示三種可能的線性運動自由度及其對應的旋轉自由度;透過結合線性平移軸與旋轉軸(如圖 3 和圖 4 所示),即可實現全部六個自由度的運動控制。

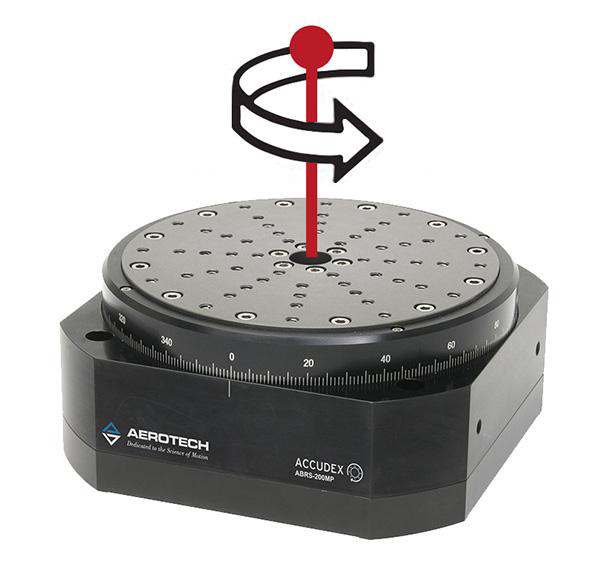
應用量測技術,能讓設計師精確量測這些運動軸的「精確程度」,無論是評估單一軸的獨立效能,或是在空間中特定點評估多軸組合的綜合表現;量測結果將可驗證此定位系統是否能達到其設計所要求的幾何規格。
如何量化這些量測值
在業界,存在一套公認的標準方法用以量化電動定位系統的效能;這些方法通常稱為定位規格,可用來量化系統的靜態與動態運動特性;這些效能規格之所以被業界廣泛接受,是因為它們可藉由標準化的量測技術進行實際量測與驗證。
首先,最常用以量化定位系統效能的兩項關鍵規格是運動的精度 (accuracy) 與重複性 (repeatability);精度根本上量測的是系統達到的最終位置與指令目標位置之間的接近程度;而重複性則量測在一系列相同的運動指令下,系統每次達到的最終位置之間的一致性程度;圖 5 直觀地展示了這個概念;圖中每個點的「指令位置」均設定在靶心;任何偏離靶心的實際落點位置,皆反映了精度與重複性的誤差。
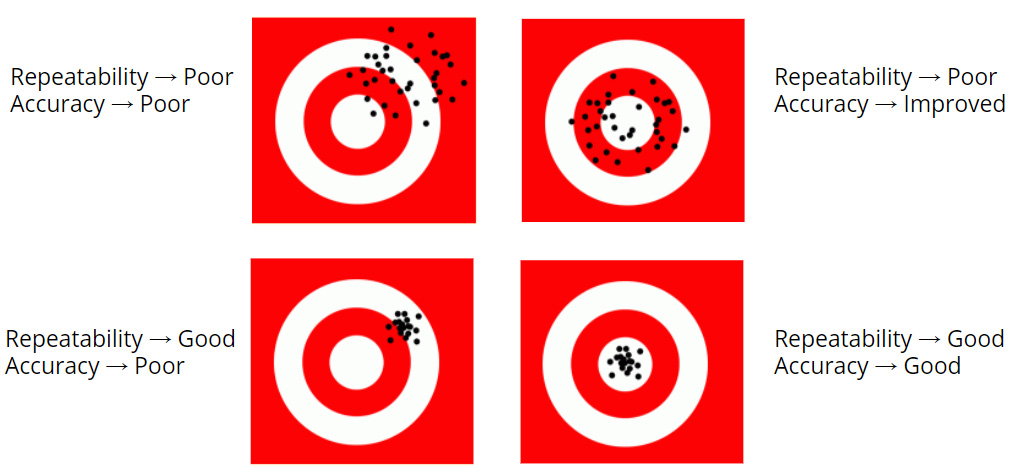
精度與重複性通常是針對機械定位器設計移動方向的單一軸向規格;此方向稱為「軸向 (on-axis)」方向;舉例來說,設計師可以讓一個機械線性定位器移動 50 公釐;;若該定位器實際移動了 50.5 公釐,則其軸向精度誤差為 0.5 公釐;此軸向精度誤差被視為該機械系統的一種誤差來源;正是這些誤差來源的存在,導致所有定位系統都無法完美地從 A 點移動至 B 點。
理解一個關鍵概念至關重要:單一機械定位軸存在多種誤差來源;儘管理論上,該軸被限制僅在單一自由度上運動,但在實際運作中,當軸在其行程範圍內移動時,會伴隨產生許多其他非預期的寄生運動;事實上,每個機械定位軸總共存在六種與運動相關的誤差來源。
其中一種誤差來源即為前述討論的軸向誤差 (on-axis error);另外五種則屬於「離軸 (off-axis)」幾何誤差;圖 6 與圖 7 分別展示了線性軸與旋轉軸的「離軸」誤差類型。
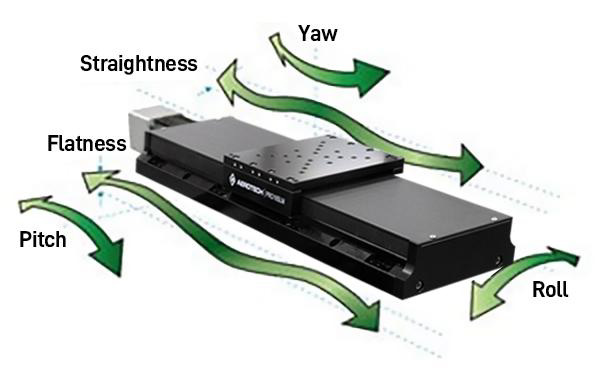
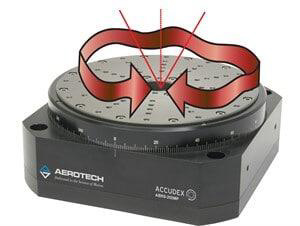
將一個多軸定位系統中所有軸的軸向與離軸誤差來源彙整於表格中,可以清晰地呈現各軸誤差之間的相互關聯性;圖 8 為一個六軸定位系統的示意範例,而表 1 則列出了此系統中各軸相對於其他軸的潛在誤差來源;由於每個軸具有六個可能的誤差來源,一個包含六個軸的定位系統理論上將存在總計三十六種誤差來源;其中任何一種誤差來源,都可能對定位系統達成其原始設計目標效能的能力構成負面影響。
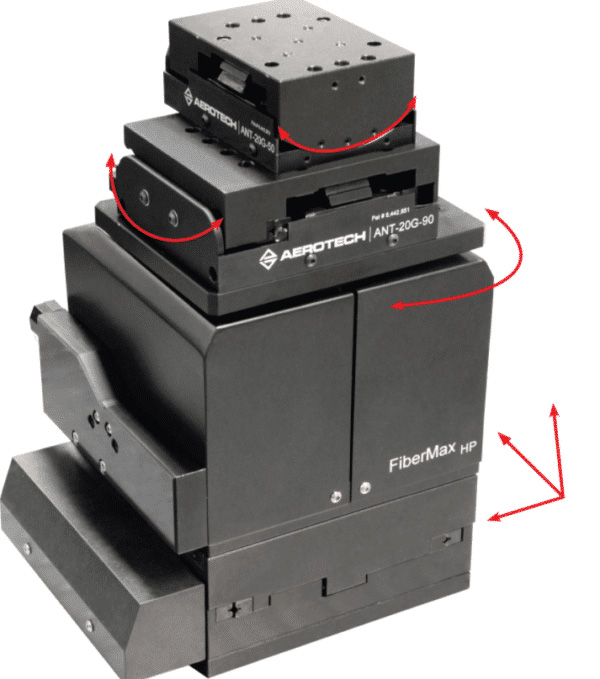
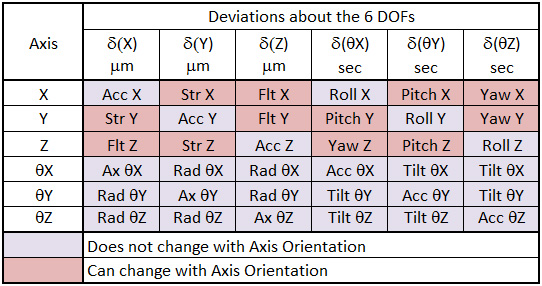
最後,表 2 概述了 Aerotech 客戶最常要求我們運用量測技術來進行評估的定位系統規格;根據電動定位系統的具體應用場景與客戶需求,某些特定規格的重要性會高於其他規格。
表 2. 運動系統中常見的其他誤差來源。
規格 |
目的 (此規格用於判定...) |
軸向精度 |
沿平移或旋轉軸方向,指令位置與實際量測位置之間的差異量值。 |
軸向重複性 |
在執行多次相同的運動循環後,沿平移或旋轉軸方向,指令位置與各次實際量測位置之間的變異範圍。 |
離軸平面度誤差 |
當沿直線進行平移運動時,實際運動軌跡在垂直方向上偏離理想平面的誤差量。 |
離軸直線度誤差 |
當沿直線進行平移運動時,實際運動軌跡在水平方向上偏離理想直線的誤差量。 |
離軸滾動/俯仰/偏擺誤差 |
當沿直線進行平移運動時,實際姿態相對於理想直線產生的角度誤差量。 |
離軸軸向誤差 |
當旋轉定位器繞其旋轉中心旋轉時,沿旋轉軸方向產生的位置誤差量。 |
離軸徑向誤差 |
當旋轉定位器繞其旋轉中心旋轉時,垂直於旋轉軸方向產生的位置誤差量。 |
離軸傾斜誤差 |
當旋轉定位器繞其旋轉中心旋轉時,其旋轉軸相對於理想旋轉軸的角度偏差或「擺動 (wobble)」量。 |
離軸偏擺度 |
當旋轉定位器繞其旋轉中心旋轉時,其特定表面(例如安裝面或導引孔)所呈現的總位移量;此值與軸向或徑向誤差不同,因其量測的是實際物理表面,而非理論旋轉軸;例如導引孔和旋轉平台表面的偏擺度。 |
軸向最小增量運動 |
系統能夠實現並可被明確辨識的最小運動步長;此為定位系統能夠進行的最小移動量的物理解析度。 |
軸向速度誤差 |
當定位系統執行特定的運動輪廓 (move profile) 時,指令速度與實際量測速度之間的差異。 |
軸向加速度誤差 |
當定位系統執行特定的運動輪廓時,指令加速度與實際量測加速度之間的差異。 |
機械對準 |
在一個多軸定位系統中,兩個或多個機械軸之間的實際裝配未對準量。 |
為何運動量測學至關重要
運動量測學使設計師能夠深入理解並特性化 (characterize) 他們所建構的依實作 (as-built) 機械系統,從而為後續的效能改進奠定基礎;這些改進涵蓋多個層面,例如實現更高精度的定位控制,或是透過優化設計來降低定位系統的製造成本;更重要的是,一旦運動效能能夠透過量測學進行精確量測,便存在相應的方法來主動預先補償並消除不期望的運動誤差;圖 9 展示了一個典型的案例,說明在補償了可量測且具備重複性的誤差來源之後,系統效能獲得顯著改善的結果。
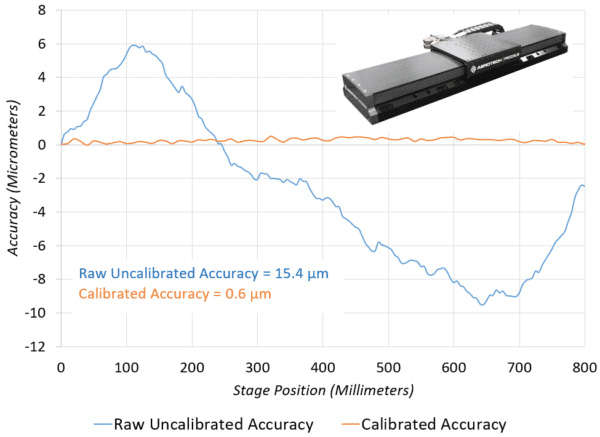
在工業應用領域,量測定位效能尤為關鍵,因為它能清晰地反映出電動定位系統在實際生產環境中的可再現性 (reproducibility);提升並驗證再現性有助於確保大規模生產的產品均能符合一致的公差要求,同時也能確保自動化製程能夠持續穩定運行,減少昂貴的人工介入需求;若缺乏透過量測學對定位系統能力的評估,製造商在試圖複製和擴展其電動自動化製程時,將難以獲得可靠的效能預期;此外,運動量測學亦可作為一種具公信力的驗證手段,用以確認電動定位設備的製造商是否確實達到了特定應用所要求的運動效能標準。
Aerotech 透過實施嚴謹的量測程序並保證所交付設備的效能規格,有效降低客戶在導入與使用上的風險;具體作法是在設備製造完成後,實際量測其定位效能,藉此明確證明該設備滿足客戶所提出的具體要求。
如何運用量測技術執行運動量測
以下介紹的技術將側重於針對定位設備的線性軸與旋轉軸,進行單軸或多軸組合的運動量測。
整合正確的邊界條件
執行運動量測所得的結果,其參考價值高度依賴於測試條件是否能真實反映電動定位系統最終的實際安裝與使用情境;表 3 所列的各項因素,都必須確保其與定位系統預期的工作條件完全一致;倘若測試條件與實際使用條件存在差異,那麼依測試 (as-tested) 所得的效能數據與依使用 (as-used) 的實際表現,很可能出現顯著的落差。
表 3. 執行量測測試時,測試設置必須整合的重要考量因素。
執行量測時需匹配的邊界條件 |
定位設備所承載的酬載 (payload)特性,包括其質量 (mass)、重心 (Center of Gravity, CG) 位置、轉動慣量 (inertia) 以及剛性 (stiffness) 特徵。 |
設備將實際運作的環境因素,涵蓋溫度變化範圍與濕度條件。 |
設備在應用中需要再現的動態特性,即運動輪廓 (motion profile),包括速度、加速度等參數。 |
定位設備將固定安裝於其上的基座結構的特性,例如其平整度與剛性。 |
製程中對位置或姿態最為敏感的方向;必須釐清是製程工具在移動,還是被加工物件在移動,因為這將決定量測基準件 (metrology artifact) 的放置位置。 |
酬載或工具在三維空間中執行任務的實際工作位置。 |
表列的最後一項條件,對於精確重現設備最終應用情境尤為關鍵;原因在於,當定位應用的實際工作點 (work point) 或稱關注點 (point of interest),與提供回饋訊號給閉迴路控制系統的量測裝置之間存在空間上的偏移時,會引入另一種特定的誤差來源。
如圖 10 所示,這種因偏移產生的誤差稱為阿貝誤差 (Abbe error),其誤差量值會隨著工作點偏移量的增加而成比例放大;因此,設計師務必準確理解製程發生的實際空間點,並在該特定位置執行量測,這點至關重要。
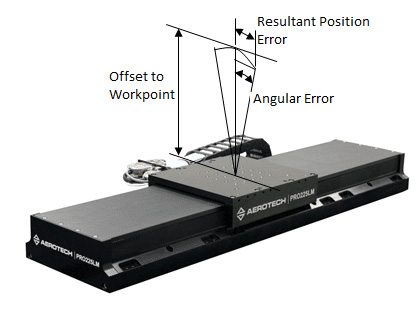
圖 10. 圖示說明由於工作點的偏移量,以及定位器自身固有的角度誤差,共同導致產生的最終定位誤差;由阿貝誤差所引起的定位誤差,將同時影響系統的軸向與離軸規格表現。
線性運動量測學
目前針對線性定位軸進行精密量測,最為廣泛採用的方法是使用雷射干涉儀 (laser interferometer);如圖 11 的設置所示,將一個移動光學元件(通常是反射鏡或角隅稜鏡)安裝於定位器的平移運動部件上,同時將一個固定光學元件(包含分光鏡與參考反射鏡)作為靜態參考基準,安裝在定位器本體與雷射光源之間。
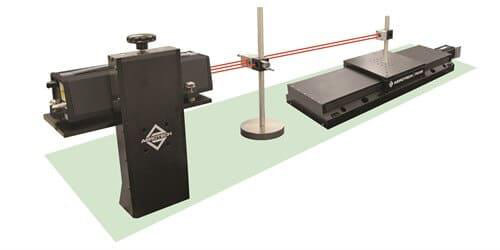
當雷射光束抵達固定光學元件時,會被內部的分光鏡 (beam splitter) 分為兩路;其中一路光束被安裝於固定光學元件支架上的逆向反射器 (retroreflector) 直接反射回雷射接收端,作為參考光路;另一路光束則穿透固定光學元件,行進至安裝在移動定位器上的移動光學元件處被反射,形成量測光路;當兩路雷射光束最終都返回雷射單元的接收器時,它們之間的光程差會導致相位移 (phase shift),進而產生特定的干涉圖樣 (interference pattern);透過精密分析此干涉圖樣的動態變化,即可準確推算出平移定位器的絕對位置;此基本原理可搭配不同的光學組件配置,用以量測設計師所關心的各種效能規格;例如,可在定位器的平移部件上加裝特殊的光學元件與稜鏡 (prisms),來量測其他類型的誤差來源,諸如直線度誤差 (straightness error) 或平面度誤差 (flatness error);在某些特定應用中,也會採用自動準直儀 (autocollimator) 這類角度量測設備,來量測如俯仰 (pitch) 和偏擺 (yaw) 等角度誤差。
線性量測測試的輸出結果,通常是呈現定位器在其完整運動行程中,各位置點所表現出的誤差量資料;具體量測的是哪一種誤差來源,取決於所選用的量測基準件 (artifact) 以及整體量測設置的配置;圖 12 描繪了一張典型的精度與重複性結果圖,顯示了定位器在正向與反向兩個行程方向上移動時,由干涉儀所記錄的誤差數據;Aerotech 的標準做法是取正向與反向運行中所出現的最大誤差值,將兩者絕對值相加,以此報告該軸的總精度誤差;而 Aerotech 定義的重複性,則是以定位器在整個行程範圍內,任何一個量測點上,正向與反向兩次運動所達位置之間的最大差異量值來計算。
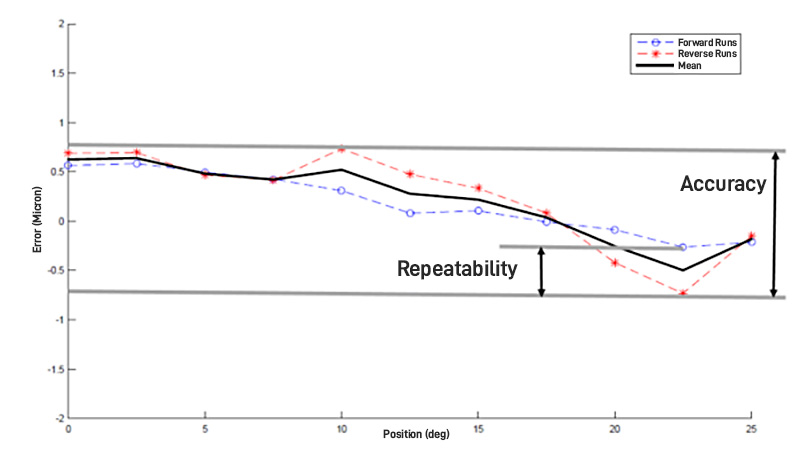
雷射干涉儀若使用得當,其量測解析度可達到次奈米 (sub-nanometer) 等級;要實現如此高的解析度,必須遵循多項最佳作業實踐規範;首先,維持環境的穩定性極為關鍵,因為溫度變化、濕度波動以及空氣擾動(氣流)都會干擾雷射干涉儀設置所量測到的相位偏移,進而影響結果準確性;許多情況下,為了確保環境穩定性,不得不縮短測試時間,例如減少採樣點數,讓整個量測過程能在數分鐘內完成,而非數小時;雖然加速測試會犧牲部分量測資料點的密度,但有時這是獲取未受環境變動干擾之可靠結果的必要手段。
其次,固定光學元件與移動光學元件之間,那段不存在相對運動的光路徑,被稱為死路徑 (dead path);雷射系統的環境補償機制(如空氣溫濕度補償)僅能在存在相對運動的有效量測光程上發揮作用,因此必須盡可能縮短死路徑的長度,以降低環境擾動對此段固定光程的影響。
最後,雷射光束必須精確對準預定的光學路徑,將餘弦誤差 (cosine error) 降至最低;如圖 13 所示,當雷射光束未能完全平行於實際運動軸線時,會引入餘弦誤差,此誤差會隨著線性定位系統的量測行程增加而放大。
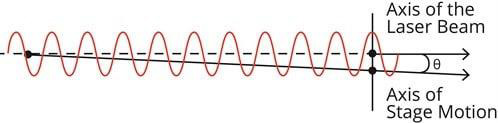
圖 13. 圖示說明雷射干涉儀量測設置中可能產生的餘弦誤差。
旋轉運動量測學
旋轉定位裝置的效能量測,通常採用與線性定位裝置不同的技術方法;一般較少使用雷射干涉儀作為主要的量測工具;自動準直儀 (Autocollimators) 與電容式感測器 (capacitive sensors) 是此領域最為常見的量測設備。
針對旋轉定位器的軸向精度與重複性量測,一種標準的技術是主軸比較法 (master-axis method);此方法中,會將一面高平整度的反射平面鏡 (reflective flat mirror) 固定於待測旋轉定位器的旋轉面上;接著,設置一台自動準直儀,使其能夠精密偵測該平面鏡發生的極微小角度變化;然後,將待測的旋轉定位器安裝固定於另一台精度極高的旋轉定位器之上,後者被稱為主軸 (master-axis) 或參考軸。
量測過程中,當待測旋轉定位器旋轉一個特定的角度時,主軸會以完全相同的角度,但沿相反方向進行同步旋轉;圖 14 展示了一套典型的旋轉校準器主軸系統以及與其配合使用的自動準直儀設備。
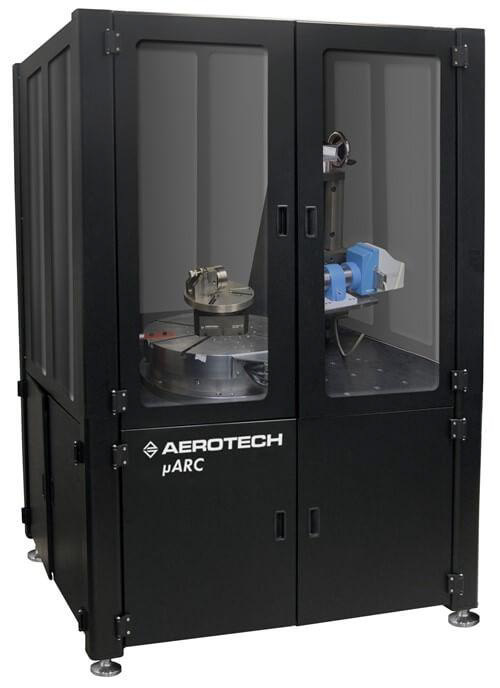
此方法的基本假設是主軸自身具有近乎完美的精度,因此由自動準直儀所量測到的任何角度偏差,皆可歸因於待測旋轉定位器的自身不精確性;這就使得選用一個具有極高精密度的主軸變得至關重要;為此,Aerotech 自行研發並測試了專用的主軸系統,用於此類精密量測,其精度可達 0.6 微弧度(小於 0.12 角秒),並且具備優異的長期穩定性。
如同線性量測的結果呈現方式,旋轉定位器的測試報告同樣會展示定位器在其整個運動行程範圍內的位置誤差分佈;圖 15 為一個旋轉定位器測試結果的量測圖範例;對於 Aerotech 的旋轉定位器,其總精度通常被定義並報告為,在整個測試行程中,所記錄到的最大誤差值與最小誤差值之間的絕對差值;而重複性則定義並報告為,在行程範圍內任何一個特定的角度位置上,正向運行與反向運行兩次量測結果之間的最大誤差差異量。
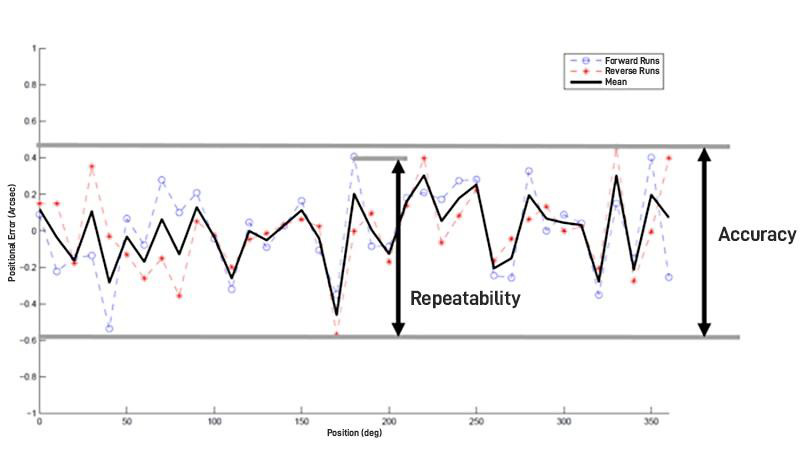
若要量測由旋轉定位器產生的離軸誤差 (off-axis errors),最普遍採用的方法是使用一個精密研磨的標準球體作為測試基準件 (test artifact),並搭配一個或多個電容式探頭 (capacitive probe(s)) 作為量測裝置,如圖 16 所示配置。
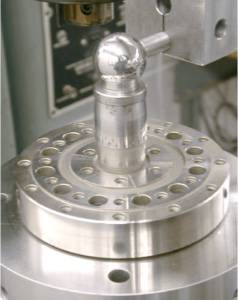
這類設置能夠量測如軸向誤差 (axial error) 和徑向誤差 (radial error) 等誤差運動;如果需要量測的是特定表面的偏擺度 (runout),則可以使用電容式探頭或電子式指示器 (electronic indicator) 直接量測待測表面的實際跳動量;關於誤差運動與偏擺度之間定義的差異,可回顧參考表 2 的說明。
這類量測所得的數據結果,可用於分析並判斷被測誤差運動中的可重複 (repeatable) 與不可重複 (non-repeatable) 成分;可重複的誤差成分稱為同步誤差 (synchronous error),它通常與旋轉角度呈週期性關係;而不可重複的誤差成分則稱為非同步誤差 (asynchronous error),它表現為隨機性波動;從圖 17 展示的典型誤差運動圖中可以看出,同步誤差在每次完整旋轉後會呈現基本相同的軌跡路徑,而非同步誤差則像是圍繞著這個旋轉軌跡的隨機雜訊帶 (noise band);Aerotech 通常將總誤差運動表示為,在旋轉定位器完整行程中,同步與非同步誤差兩者峰值之和或綜合考量的最差情況值。

如何運用運動量測學成果來滿足技術規格要求
當透過量測發現存在不期望的運動誤差後,存在多種方法可以對其進行補償;當然,一旦量測結果顯示定位系統的效能誤差過大,一種直接的改進方式是謹慎地重新組裝調整機械結構部件;或者,可以考慮重新設計系統,例如採用更高精密等級的導軌表面 (guide surfaces),或是選用更準確且安裝位置更優化的回饋系統 (feedback systems) 以改善閉迴路控制效果。
另一種無需進行硬體重新設計的方法,是運用校正技術 (correction technique);其原理是將量測得到的運動誤差值,從運動控制器 (motion controller) 發出的指令位置值中予以減除,如圖 18 的概念所示;採用誤差校正是一種可靠且成本效益相對較高的技術手段,能夠快速有效地補償定位系統中可能存在的許多系統性誤差。
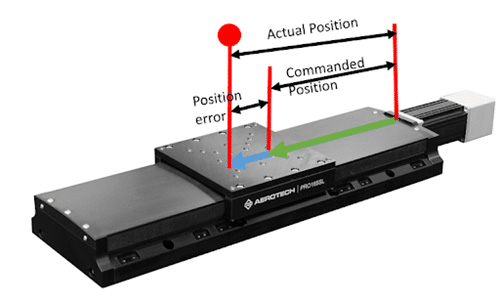
最為普遍採用的校正方法,是針對線性系統,在其實際工作點 (work point) 位置量測其軸向誤差 (on-axis error),然後建立一個校正數據表(如圖 19 所示範例);這個表格會被載入運動控制器中,控制器依據此表,將對應位置的量測誤差分量從原始的指令位置訊號中扣除;為了達到最佳補償效果,此校正值應由運動控制器以低延遲方式主動即時地應用於運動指令。
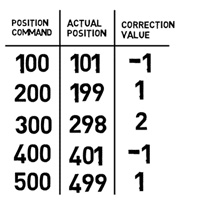
然而,許多情況下,僅僅補償單一軸的軸向誤差,往往只處理了影響運動系統整體效能的部分潛在誤差來源;這在多軸定位系統中尤其常見,因為隨著系統自由度數量的增加,各軸的運動誤差會相互疊加,產生所謂的公差累積 (tolerance stackups) 效應;回想先前提及,每個獨立的運動軸都存在其自身的六種誤差來源,當多個軸組合在一起時,這些誤差會產生複合效應。
但好消息是,一旦這些複雜的誤差能夠透過量測技術被準確地量測出來,設計師通常可以利用定位系統中其他軸的運動能力,來相互補償彼此的誤差來源;這種技術被稱為交叉軸補償 (cross-axis correction);舉例來說,觀察圖 20 中的 XY 軸堆疊式定位器,當下方的 X 軸移動時,它會不可避免地表現出直線度誤差 (straightness error),這個誤差可以透過雷射干涉儀的量測設置精確量測得到;接著,可以將這些量測結果製成校正表,並指令上方的 Y 軸根據 X 軸的當前位置,進行微小的補償運動,用以抵銷 X 軸在移動過程中的直線度誤差;運用交叉軸補償方法,能夠顯著地降低例如直線度這類的離軸誤差。

另一種運用量測學來補償定位誤差的進階策略,是在系統中整合原位回饋 (in-situ feedback) 感測器,並將其訊號直接用於閉迴路運動控制器;例如,我們可以將原本用於離線量測校準的雷射干涉儀量測系統,直接整合到定位系統的最終設計之中,使其能夠對關鍵位置進行連續、即時的量測;一個典型的應用場景是,需要在一個遠離運動軸承與編碼器的較高工作平面上,減小 XY 平面內的定位誤差。
如圖 21 所示,假設實際的製程工作點位於一個平面真空吸盤 (flat vacuum chuck) 的表面上方;
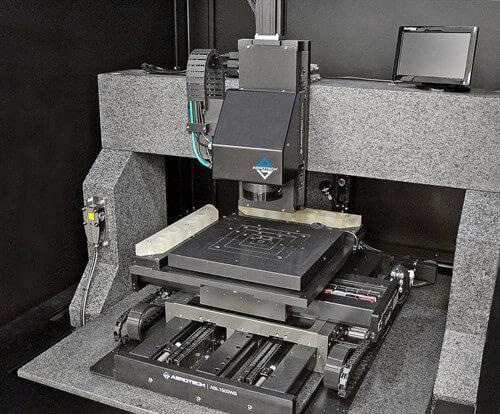
由於這個工作高度(吸盤表面)相對於承載運動的軸承表面以及傳統編碼器回饋 (encoder feedback) 的量測位置存在顯著的高度差,因此在吸盤表面處必然會受到阿貝誤差 (Abbe error) 的顯著影響;此時,可以導入一套二維 (2D) 雷射干涉儀系統,直接且即時地量測吸盤表面在 XY 空間中的實際位置;將此高精度的即時位置回饋訊號,直接用於閉迴路控制,如此一來,定位系統便能有效克服阿貝誤差效應(同時也可能間接消除了某些次級誤差效應,例如偏擺誤差 (Yaw errors))。
焦點產品
Aerotech 六軸 (6-DOF) Hexapods 定位系統
Aerotech 的六軸 (6-DOF) Hexapods 定位系統(亦稱為 Stewart 平台)為市場提供了高性能的六自由度運動控制解決方案,這類系統以其領先業界的保證精度著稱,Aerotech 公開其規格與性能曲線,確保達到次微米級的定位精度,甚至可執行 20 奈米 (nanometer) 級別的步進運動,並經過外部設備驗證。
核心優勢與應用領域:
Aerotech Hexapods 系統的核心優勢在於其:
- 超高精度:
提供市場上最精確的運動控制技術之一,並有數據保證。 - 可靠性:
設計堅固耐用,能夠適應全天候 (24/7) 的高負載工業運行環境。 - 單一控制器:
透過 Aerotech 強大且使用者友善的單一控制器即可管理所有運動軸,並支援即時運動模擬與視覺化,簡化了編程、整合與操作的複雜性。
這些高性能的六軸平台適用於對精度、穩定性及多自由度運動有嚴格要求的應用,例如:
- 光子器件操作與對準
- 半導體製程與精密檢測
- 航太與衛星傳感器測試
- 同步加速器與光束線樣品操作
- X 射線繞射
- 醫療與生物技術領域的高精度運動控制
系列產品與客製化能力:
Aerotech 提供了包括 HEX150、HEX300、HEX500 系列在內的標準化六軸平台產品線,可滿足從 7.5 公斤到 200 公斤等級的不同負載能力需求;不僅如此,面對標準品無法滿足的特殊應用,Aerotech 及台灣合作夥伴 奧創系統 還提供專業的客製化六軸 (6-DOF) Hexapods 定位系統與解決方案,服務範圍涵蓋特殊的安裝介面、線纜配置、行程範圍調整乃至真空環境兼容性等深度設計修改,以精確滿足客戶的獨特需求。
結論
顯而易見地,執行運動量測是深入理解電動定位系統效能不可或缺的關鍵步驟;確保在量測測試的設置階段,施加恰當且符合實際工況的邊界條件,並採用正確有效的技術手段來執行量測,將能產出極具價值的量測數據資料;這些精確的量測數據,隨後即可被用來有效補償定位系統中固有存在或由其他因素引入的位置誤差;若能量測方法應用得當,不僅能顯著提升定位系統的整體效能,更能有效降低該系統在實際應用中無法滿足規格要求的風險;在 Aerotech,我們擁有深厚的專業知識與豐富經驗,能夠為客戶精確理解並執行所需的各項量測任務。
作者簡介
RJ Hardt 現任 Peak Metrology 公司總裁,該公司隸屬於 Aerotech 旗下,專注於高精度表面量測設備的研發與製造;他在運動控制與自動化技術領域擁有超過十年的豐富實務經驗,長期直接與客戶合作,協助客戶導入並應用相關技術解決方案。