非接觸式位移量測技術於精密運動控制系統之原理與應用
精準定位,源於先進非接觸量測技術
“比較四大非接觸感測技術(渦電流、電容、雷射、共軛焦)於高精度定位與表面特性量測之應用”
非接觸式位移感測器主要應用於表面或製程不允許接觸,且同時要求極高量測精度的場合;在眾多技術中,電容式、共軛焦、渦電流及雷射三角測距感測器因其在整合精密運動系統應用中的可靠表現而廣受肯定,市面上存在多種設計的非接觸式感測器;然而,一個重要的考量是,當對精度的要求提升時,感測器的有效量測範圍通常會隨之顯著縮減。
儘管存在量測範圍上的限制,市場上仍提供足夠多樣化的產品,讓使用者能針對特定應用情境選擇最合適的感測器;以下內容旨在簡述各項關鍵的位移感測技術,以利於使用者進行技術評估與選型;必須強調的是,最終系統所能達成的量測精度,並非僅由感測器單獨決定,而是感測器本身、後端處理電子電路、訊號處理演算法以及操作環境條件等多重因素綜合影響的結果。
渦電流量測原理
從物理原理嚴謹分類,渦電流感測原理 (Eddy-Current Measuring Principle) 應屬於電感式量測的一種;透過渦電流進行量測的核心機制,是利用振盪電路能量的轉移,此能量被用來在導電材料中引發渦電流 (eddy currents);具體來說,感測線圈被施加交流電,進而在線圈周圍產生變化的磁場。
依據法拉第感應定律 (Faraday’s Law of induction),若此磁場範圍內存在導電物體,將在該物體內部產生渦電流;接著根據冷次定律 (Lenz Rule),這些渦電流自身產生的磁場,其方向會與原始線圈的磁場相反,進而改變線圈的總體阻抗。此阻抗變化量與感測器到目標物體的距離有明確對應關係,經過轉換後可輸出為絕對距離讀值。
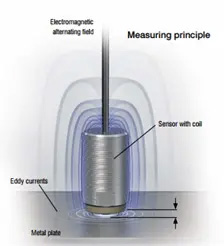
渦電流感測器的適用對象為所有具備鐵磁性或非鐵磁性特質的導電材料,並具備穿透非導電介質進行量測的能力,其感測頭通常能實現小型化設計;渦電流感測器特別適合應用於環境條件相對惡劣,且對精度要求屬於「中等」等級的場景;其對於髒污、壓力變化及極端操作溫度的高度耐受性是關鍵的性能優勢,使其成為理想選擇,例如在雷射加工製程中,運動系統需利用感測器回饋進行即時的焦點高度調整控制。
值得注意的是,感測器的輸出訊號特性與線性度會受到目標材料的電氣與磁性參數影響,因此針對不同的待測材料,感測器需要進行專門的校準。此外,感測器的探頭直徑以及有效的量測光點直徑,會隨著量測範圍的增加而變大;不過,此特性有時也可被利用,透過較大的感測面積來取得目標表面的平均形貌資訊。
電容式量測原理
電容式量測原理 (Capacitive Measuring Principle) 是建立在理想平行板電容器的運作模型之上;當一個頻率恆定的交流電流流經感測器探頭形成的電容器時,感測器上量測到的交流電壓幅值,會與感測器探頭到目標導體(接地電極)之間的距離呈現明確的比例關係;在實際設計中,感測器常採用保護環電容器 (guard-ring capacitors) 結構,這種設計有助於達成近乎理想的線性響應特性。電容式感測器除了量測導體外,亦可用於量測絕緣材料的距離或厚度。
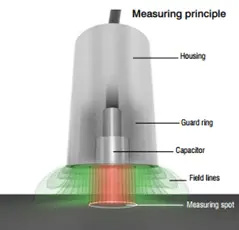
電容式感測器的主要優勢在於,對於所有導電目標物,其靈敏度和線性度基本保持恆定,同時展現出優異的溫度穩定性與訊號穩定性。電容式感測器能夠達到次奈米等級的解析度,並維持良好的線性度。此類感測器特別適用於量測相對潔淨環境中的大面積平坦表面;因此,應避免用於量測區域可能產生加工煙霧 (plume) 或其他污染物的雷射應用環境。
雷射三角測距量測原理
雷射三角測距 (Laser Triangulation Measuring Principle) 技術的運作方式是將一束經過準直的雷射光束投射到目標物體表面;從目標表面漫反射回來的光點,會透過一個成像透鏡聚焦到一個感光元件陣列上,此元件通常是 CCD (感光耦合元件) 或 CMOS (互補式金屬氧化物半導體) 感測器,或者是 PSD (位置感測偵測器) 元件,反射光束的接收強度會依目標材料的表面特性而變化,感測器到目標物體的距離,是根據反射光點在接收元件上的成像位置,透過幾何三角關係計算得出;原始位置資料會在感測器內部控制器中進行處理與運算,最終透過不同的通訊介面(如類比電壓、數位訊號等)輸出距離值。
雷射三角測距裝置的技術優點包括量測光點直徑可以很小、感測器探頭與待測物體間可容許較大的工作距離 (offset distance)、通常具備較大的量測範圍,以及量測結果幾乎不受目標材料種類的影響;然而,其量測精度容易受到目標表面光澤度(光亮或霧面)的影響,且要求雷射光束的傳播路徑必須維持在潔淨、無任何遮蔽物的環境中;此外,相較於共軛焦、電容式及渦電流感測器,雷射三角測距感測器的物理尺寸通常較大,並且在量測高反射性表面時,需要進行特殊的感測器角度對位;若待測物表面形貌極度複雜,可能導致反射光束無法有效返回感測器接收端,從而造成量測資料的遺失或中斷。
儘管存在這些限制,雷射三角測距技術仍可提供一種成本效益高且能快速進行表面輪廓掃描的解決方案;但必須再次強調,該技術不適用於光束路徑中可能出現碎屑、粉塵或其他污染物的應用環境。
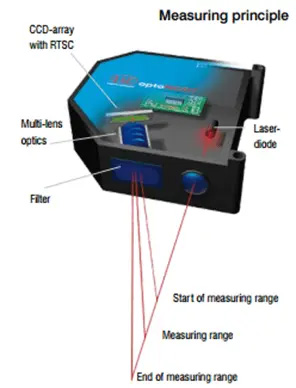
共軛焦色散感測器量測原理
共軛焦色散量測原理 (Confocal Chromatic Sensor Measuring Principle) 利用多色光(通常是白光)作為光源,此光源位於控制器內部,其發出的光線透過光纖傳輸至感測器探頭;探頭內部的精密光學透鏡組經過特殊設計,使得白光在沿著光軸的縱向傳播時,會因為受控的色像差 (chromatic aberration) 而被分解成依序排列的單色光波長;這組透鏡將分解後的光線聚焦投射到目標物體表面,依據感測器探頭與目標表面的實際距離,將會有一個特定光譜顏色(即特定波長)的光恰好完美聚焦在表面上;在感測系統中,正是這個精確聚焦於目標上的光的波長被用於進行距離量測;從目標表面該點反射回來的光線,再經由另一組光學結構成像到一個光敏偵測元件上(例如光譜儀),在此處偵測並分析反射光的光譜顏色。透過原廠校準程序,每一個特定的波長都被賦予了一個精確對應的距離值。
這個獨特的量測原理使得共軛焦色散感測器幾乎能夠量測所有類型的表面,包括透明材料或半透明材料。其主要優勢包括:可達到極高的量測解析度(達到奈米等級)、量測結果基本上不受目標表面材質影響、擁有極小且恆定的量測光點尺寸,以及光束路徑設計緊湊。其應用上的限制則主要有:感測器探頭與待測物體之間的工作距離相對較短、與雷射感測器類似,要求光束路徑中維持潔淨的環境,以及相對較高的購置成本 — 此類感測器通常比本文討論的其他幾種技術價格更高。
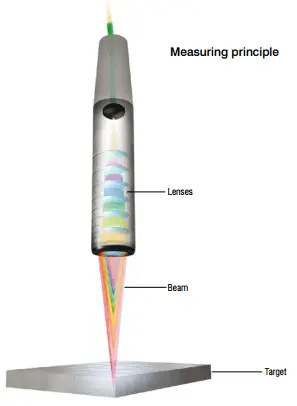
結合先進運動控制器功能實現位移感測應用
自動對焦 – 垂直高度的精密控制
先進的運動控制器 (Autofocus – Precise Vertical Height Control),例如 Aerotech 的 Automation1 平台,具備啟用外部追蹤迴路的能力,此迴路能與系統中的伺服馬達或步進馬達緊密協同運作;在這種架構下,位移感測器便可作為此高度控制迴路的主要回饋裝置,典型應用是實現對系統內某個軸(通常是 Z 軸)垂直高度的精確控制;感測器輸出的類比電壓訊號(與量測距離成比例)被直接連接至運動控制器的類比輸入埠,作為即時的高度回饋;控制器內部的自動對焦 (Autofocus) 回饋演算法通常採用一個簡化的 PID (比例-積分-微分) 控制迴路,經過適當參數設定後,能夠持續、動態地維持感測器探頭與目標表面間的預設高度 — 例如,應用於顯微鏡或雷射加工頭的自動對焦,或是要求探針穩定接觸目標位置的應用;此外,通常可以設定一個反應死區 (deadband),以防止控制軸因微小擾動而不斷進行微調(稱為 hunt 現象)。
為了確保運動平順性,可以透過設定控制器的加速度限制 (Acceleration Limiting) 功能,來約束軸向的最大加速度;如此一來,因啟用自動對焦功能而可能導致的位置命令值急遽變化,便可有效減緩或消除。同理,也可以透過設定速度鉗位值 (speed clamp value) 來指定最大允許追蹤速度。為了處理實際應用中可能遇到的表面不連續情況(如孔洞或邊緣區域),可以設定追蹤範圍的上限與下限,以防止控制軸因遭遇這些區域而產生過大的高度波動。
位置同步輸出 (PSO) 功能應用
特定的運動控制器,如 Aerotech 控制器,具備接收最多三個獨立編碼器訊號輸入的能力,並能將這些訊號整合,實現基於一維、二維或三維空間路徑的高精度追蹤;在沿著此定義路徑運動的過程中,控制器能夠產生與運動位置高度同步的脈衝觸發訊號,此功能稱為 PSO (位置同步輸出, Position Synchronised Output)。PSO 的典型應用包括:精確調變工業雷射的輸出功率(例如在雷射雕刻或打標中)、觸發外部硬體裝置(如高速相機或資料擷取卡),或是同步感測器輸入端的資料擷取。由於 PSO 功能是透過專用硬體線路實現,而非依賴軟體時脈,因此具有極低的觸發抖動和極低的延遲特性。
PSO 功能主要由兩個核心邏輯區塊構成:距離計數器和脈衝產生器;距離計數器負責監控一個或多個軸的運動距離,當累計運動距離達到預設值後,便會產生一個「觸發事件 (firing event)」;此事件訊號可以直接傳送給感測器的電子控制單元,命令其在該精確位置點記錄下當時的位移量測資料。觸發事件之間的距離可以是固定不變的,也可以是依據預先載入的陣列資料而變化。運用此功能,便能沿著運動路徑建立連續的表面輪廓資料,或是針對待測工件上的特定關注特徵進行重點式量測。
由於 PSO 資料觸發可以基於一維路徑,因此大多數 Aerotech 運動控制器硬體都能執行簡單的線性掃描應用,例如光柵式掃描 (rastering);若需要進行二維 XY 平面的工件資料擷取,則可選用具備雙通道 PSO 功能的控制器型號;而對於更複雜的三維空間輪廓或螺旋路徑掃描,則需要具備三通道 PSO 功能的控制器來實現。
運用驅動資料擷取功能進行高速資料蒐集
在 Automation1 控制器平台上,可透過 AeroScript 程式語言調用 Drive Data Capture 功能,此功能可與 PSO 協同運作,將量測資料直接記錄在運動控制器內部的高速緩衝區,而非儲存在感測器本身的電子單元中;被擷取的通常是在 PSO 觸發事件發生瞬間的類比訊號值。以共軛焦感測器為例,擷取的類比資料除了距離值外,也可能是反射光強度,此強度資訊有時可用於判斷感測器下方工件的其他表面特性(如材質變化、塗層缺陷等)。
反向應用方面,也可以利用運動控制器的高速數位輸入埠,接收來自外部來源的觸發訊號或其他控制器內部產生的事件,來啟動資料記錄程序;同樣地,可以記錄下觸發瞬間的位移值、強度值,或是來自控制器連接的各個編碼器輸入的位置值。
以感測器輸出作為位置回饋訊號
感測器電子單元輸出的類比訊號,除了前述的自動對焦應用外,還可作為一種非傳統形式的位置回饋來源;與自動對焦模式(該模式下,馬達自身的回饋裝置,如編碼器,仍然是主要的伺服迴路回饋)不同,此模式下運動控制器可以將感測器的類比輸出直接指定為絕對位置的主要回饋來源;這種架構可以單獨使用(感測器作為唯一的位置回饋),也可以與另一個速度回饋裝置(如馬達編碼器的速度訊號)結合,形成一個串級控制迴路(感測器負責外環位置控制,編碼器負責內環速度控制);這種應用方式在以下幾種情況下特別有用:需要利用類比感測器在相對較短的行程範圍內實現極高解析度的位置回饋時;當應用場合不適合安裝傳統的馬達編碼器時;或是當感測器本身因空間限制或其他因素,無法直接安裝在最終需要精密定位的量測點時。
將編碼器回饋訊號輸入感測器電子單元
某些高階感測器的電子單元具備直接接收外部增量型編碼器 (incremental encoders) 訊號的能力,最多可同時接入三個獨立的編碼器;這使得系統能夠將高精度的運動軸位置資料(來自編碼器)與感測器量測到的位移資料以及(若適用)強度資料進行精確的時間同步記錄;運動控制器可以將連接到自身的編碼器訊號鏡像輸出 (echo-out) 給感測器電子單元;此外,若控制器配備適當的硬體介面,還可以將非增量型的編碼器(例如絕對型編碼器或特定串列通訊協定的編碼器)的訊號轉換成感測器電子單元可接受的標準增量格式。
軟體整合能力:LabVIEW/.NET 支援
現代運動控制器如 Aerotech 產品,通常會提供豐富的軟體函式庫 (libraries) 以及專為 LabVIEW 環境設計的 VI (虛擬儀器) 模組;將這些控制器提供的軟體工具,與感測器製造商提供的相應軟體開發套件 (SDK) 或驅動程式結合,開發者便能創建出功能強大、介面友善的客製化前端應用程式以及複雜的資料分析軟體。
智慧型軟體式運動控制核心
智慧型軟體式運動控制器 (iSMC) 的核心概念是將高精度的運動軌跡控制與複雜的製程邏輯控制無縫整合在單一平台之上;以 Aerotech 的 Automation1 iSMC 為例,無論是僅需編寫簡單的單軸或多軸移動指令、建構控制整套複雜自動化設備的完整應用程式,或是介於兩者之間的中等複雜度任務,這類軟體控制器都能提供高品質的自動化解決方案,有效提升設備的整體產能。
由於 iSMC 架構通常與廠商提供的使用者友善的開發環境(如 Automation1 運動開發套件)緊密整合,開發者可以快速完成系統組態設定與應用程式開發、輕鬆設定與管理各種控制週邊裝置(如驅動器、I/O 模組),並能受益於多種提升開發效率的程式設計輔助功能,例如智慧語法自動完成、即時情境式說明文件、自動化的伺服迴路調諧工具(如 EasyTune®)、編譯前的即時語法與邏輯檢查、方便偵錯的變數與 I/O 狀態監看視窗等等。
這類軟體控制器通常能在個人電腦 (PC) 硬體平台或整合於驅動器的硬體平台上運行,為使用者在規劃與部署各式各樣的運動控制解決方案時,提供了高度的系統架構彈性。
迎向精密製造新紀元:我們的雷射自動化加工系統解決方案
正如光學元件製造正從微米邁向奈米精度,現代工業對精密加工的要求已達前所未有的高度。面對小型化、複雜化與量產效率的多重挑戰,您需要的不僅是設備,更是能克服震動干擾、實現精確控制並確保長期穩定的整合解決方案。我們的雷射自動化加工系統,正是為此而生,助您在激烈競爭中脫穎而出。
高階振鏡雷射掃描與伺服雷射加工系統
結合振鏡 (Galvo) 的極致掃描速度與伺服系統的大範圍、高精度運動控制,此系統能同時滿足高速標刻、精密焊接或複雜圖案切割等多樣化需求,克服傳統單一系統在速度或範圍上的限制,實現奈米級精度下的高效產出;了解更多 >
3D Galvo 雷射掃描頭與伺服控制系統
專為三維工件與曲面加工設計。3D 振鏡掃描頭能在 Z 軸動態聚焦,搭配精密的伺服控制系統,即使在複雜的 3D 輪廓上也能實現高速、均一且精確的雷射加工,完美應對模具蝕刻、曲面標記、3D 列印後處理等挑戰;了解更多 >
三軸龍門式光纖雷射切割系統
採用高剛性龍門結構,確保高速運動下的穩定性與重複定位精度,有效抑制環境震動干擾。結合高效率、低維護的光纖雷射,為金屬板材或其他大尺寸材料提供無與倫比的切割速度與斷面品質,是實現工業級穩健性與高產能切割作業的標準配備;了解更多 >
三軸龍門式光纖雷射加工系統
延續龍門結構的穩定優勢,此系統不僅限於切割,更能整合焊接、鑽孔、表面處理等多種光纖雷射應用。提供寬廣的加工範圍與優異的承載能力,滿足您從原型製作到大規模量產的多元需求,一個平台,多種可能;了解更多 >
3D 雷射加工系統
超越傳統 2.5D 加工,此系統具備真正的多軸聯動能力,能對任意複雜的三維物件進行精密的雷射加工,無論是增材製造、精密減材還是表面改質,應對航空航太、醫療器材等領域的嚴苛要求;了解更多 >
整合式雷射加工系統
將雷射源、運動控制、視覺系統、上下料模組等完美整合於單一平台。我們提供的不僅是硬體,更是經過深度優化與驗證的完整加工流程,大幅縮短您的系統整合時間與風險,實現開箱即用的高效生產;了解更多 >
多工精密製造系統
打破單一製程限制,將雷射加工(如切割、焊接、標刻)與CNC 銑削、精密量測等工藝整合於同一系統。實現工件在一次裝夾下完成多道精密工序,大幅提升加工效率與精度,特別適用於需要複合製程的高附加價值零件生產;了解更多 >
七軸雷射動態控制系統
結合六軸機械手臂的靈活姿態與高精度線性軸或旋轉軸,提供七軸聯動的超高自由度。無論是大型複雜曲面,還是微小零件的精細加工,都能實現無死角、高動態的雷射精密控制,是應對高階雷射應用的終極解決方案,了解更多 >
雷射自動化加工系統應用比較表
下表協助快速比較不同雷射自動化加工系統的特點與主要應用場景,以便根據具體需求選擇最合適的解決方案。
系統名稱 |
主要特點與優勢 |
理想應用場景 |
高階振鏡雷射掃描與伺服雷射加工系統 |
結合振鏡高速掃描與伺服大範圍高精度運動,速度與精度兼具。 |
高速標刻、精密焊接、複雜圖案切割、需要大範圍與高精度結合的應用。 |
3D Galvo 雷射掃描頭與伺服控制系統 |
具備 Z 軸動態聚焦能力,可在複雜 3D 曲面上實現高速、均一、精確加工。 |
3D 工件、曲面加工、模具蝕刻、曲面標記、3D 列印後處理。 |
三軸龍門式光纖雷射切割系統 |
高剛性龍門結構,穩定性與重複定位精度高,適合大尺寸材料高速、高品質切割。 |
金屬板材切割、其他大尺寸平面材料切割、要求高穩定性與高產能的切割作業。 |
三軸龍門式光纖雷射加工系統 |
延續龍門穩定性,整合切割、焊接、鑽孔、表面處理等多種光纖雷射應用,加工範圍廣。 |
多元化平面加工(切割、焊接、鑽孔等)、原型製作到大規模量產。 |
3D 雷射加工系統 |
真正的多軸聯動能力,可對複雜三維物件進行精密加工(增材、減材、表面改質)。 |
複雜 3D 工件加工、航空航太、醫療器材、高精度三維結構製造。 |
整合式雷射加工系統 |
將雷射、運動、視覺、上下料等整合於單一平台,提供深度優化、開箱即用的完整加工流程。 |
需要快速導入、降低整合風險、一站式解決方案的應用、確保精確協調的奈米級製程。 |
多工精密製造系統 |
整合雷射加工與 CNC 銑削、量測等工藝,實現一次裝夾完成多道工序,提升效率與精度。 |
需要複合製程的高附加價值零件生產、減少工件重複裝夾誤差。 |
七軸雷射動態控制系統 |
結合六軸機械手臂與高精度軸,提供七軸聯動的超高自由度與靈活度,實現無死角、高動態精密控制。 |
大型複雜曲面加工、微小零件精細加工、機器人自動化產線中的高階雷射應用。 |